Key Takeaways
1. Garmin released software version 8.11 for Lily 2 and Lily 2 Classic smartwatches.
2. New features include additional watch faces and a Device Passcode tool for added security.
3. The Device Passcode requires a four-digit PIN when the watch is removed or idle.
4. Other updates include Sensor Hub (version 34.12) and GCM/Text Translations (version 8.10), with unclear user benefits.
5. The update is available for download via Garmin Express or Garmin Connect Mobile, and the watches retail from $249.99 on Amazon.
Garmin has released software version 8.11 for the Lily 2 and Lily 2 Classic smartwatches. This update comes after the February firmware version 7.10, which introduced the Body Battery TrueUp feature to these devices.
New Features and Security Enhancements
With the new software update, users of the Lily 2 series can now enjoy additional watch faces. Moreover, the smartwatches have gained access to the Device Passcode tool, which was previously available on other models like the Venu 3 and vivoactive 5. This feature enables users to set a four-digit PIN, providing an extra layer of security. The passcode will be required when the watch is detected as removed from the wrist or after being idle for a long time.
Other Updates and Uncertainties
In addition to these exciting features, there are three more updates for the Sensor Hub (version 34.12), GCM Translations (version 8.10), and Text Translations (version 8.10). However, it remains uncertain how users will benefit from these specific updates.
The software version 8.11 for the Garmin Lily 2 Series can be downloaded through Garmin Express or Garmin Connect Mobile. A recent update on the company’s forum states that this version is now available for all users of the Lily 2 and Lily 2 Classic smartwatches, which currently retails from $249.99 on Amazon.
Source:
Link
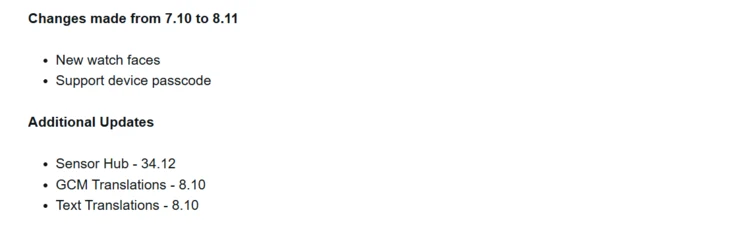